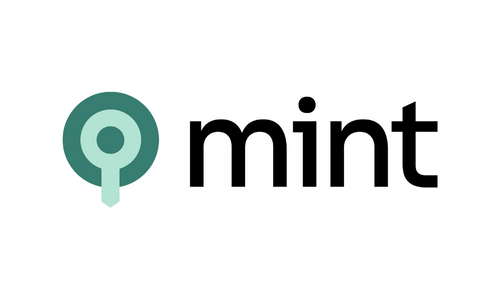
Mint Innovation is a cleantech company focused on the low carbon recovery of precious metals from electronic waste. Over the past 6 years, Mint has taken its technology from proof of concept to building a commercial scale plant in Sydney capable of processing over 3,000 tonnes of printed circuit boards per year.
Mint was co-founded by Dr Will Barker and Dr Ollie Crush, two serial biotech entrepreneurs with extensive experience in clean technology. Over the past six years they have put together a team of highly qualified chemists, engineers and business developers to commercialise this revolutionary technology across the globe.
Mint’s current R&D facility is in East Tamaki, Auckland, which houses a 1 tonne per batch pre-commercial plant. This prototype has now been scaled to a commercial scale plant in Sydney, capable of processing over 3,000 tonnes of printed circuit board waste per year. Mint’s vision is to build a recycling facility in every major city in the world, thus equipping regions with the tools to develop their own circular economy, reduce emissions and meet their sustainability targets.
Mint’s primary focus is on precious metals such as gold and palladium. These metals are critical in the production of small IT equipment such as our phones and laptops. Mint’s technology is also capable of recovering metals such as lithium, cobalt, nickel, which are critical for batteries to meet the growing demand for the electrification of the world.
As demand for metals continues, mining becomes increasingly inefficient. For example, previously a tonne of gold ore could yield 500g of gold, whereas today's mining only typically achieves 5g of gold per tonne of mined ore. Many mines are inefficient, unsustainable and often unethical as they exploit workers in developing nations. It is estimated that there is more gold available in our waste electronics than there is in virgin mines - waste electronics that form part of the urban mine containing over 80 billion USD of metallic value.
In addition to the decreasing efficiency of virgin metal mining, the incumbent method of metal recovery from circuit boards is smelting. The handful of smelters with capability are energy intensive and produce copious amounts of carbon emissions. While their process is efficient in metal recovery, recyclers and high e-waste producing cities still need to ship their e-waste to them, an activity that adds to their carbon footprint.
Mint aims to supplement supply chains by recovering critical metals from the urban mine locally, in a low carbon and low cost manner. Mint’s technology enables such localised recovery through using a combination of chemical and biological processes. The process is able to recover base metals such as tin, nickel and copper, with low concentrations of gold and palladium sequestered by a naturally occurring biomass. The recovered biomass contains near-pure gold, and this alongside other recovered metals can be directly reused for new applications.
This technology is scalable and can be inserted into existing local supply chains in cities, thus allowing the deployment of plants across the world. Mint’s technology is currently primarily focused on printed circuit boards which are present in all small IT equipment. Mint is translating its core technology to process lithium batteries, and aims to roll out this new metal recovery line at future plants on top of printed circuit boards.
With two plants in the current pipeline, Mint will be accelerating its plant deployment into Europe, US and Asia. Mint’s R&D team is working to expand its technology to recover critical metals from other potential feedstock such as catalytic converters, incinerator bottom ash
and mine tailings. As plants are built and feedstock waste stream targets expand, Mint aims to reduce the world's reliance on carbon-intensive mining and smelters by equipping cities with the tools to recover value from their own waste locally.
Contact:
Nipun Goyal
Commercial Analyst - Mint Technology
E: nipun@mint.bio
www.mint.bio