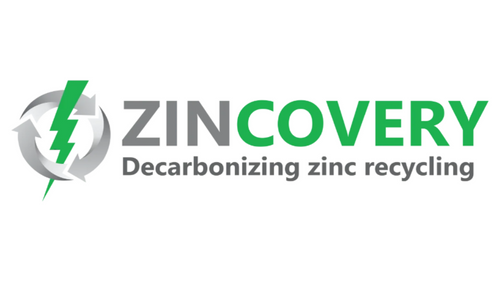
Zinc is the only major industrial metal that has a higher CO2 footprint when it is recycled than mined. Zincovery has unlocked a solution for sustainable zinc recycling from industrial wastes, with much lower emissions and production costs. We are on the way to achieving our mission of decarbonizing zinc recycling!
In 2017, Professor Aaron Marshall was approached by the galvanising industry to solve their expensive waste acid problem – containing large quantities of zinc and iron. Aaron enlisted Jonathan Ring to research technologies that could solve this problem as part of a Master’s project. Together they founded Zincovery in 2019 – winning the Callaghan Innovation C-price.
The company grew quickly to six full-time employees, carrying out a successful pivot away from the galvanising industry into the recovery of zinc from furnace dusts. These furnace dusts are a waste output of industries such as steel recycling and the production of brass and bronze. The technology has been successfully adapted for furnace dusts and proven at lab scale. The technical and market development enabled Zincovery to complete an oversubscribed second capital raise in September this year, quickly followed by Jonathan winning the KiwiNet Breakthrough Innovator Award in October. With the capital secured the team is expanding to 11 employees, ready to scale up the process and sign large commercial agreements with customers and supppliers.
The incumbent technology for zinc recycling from furnace dusts is the Waelz kiln, which incurs high production costs and produces a high level of emissions. It has been the primary method of recycling zinc with the technology servicing a number of large steel mills around the world. To feasibly operate, a Waelz kiln needs economies of scale obtained by a large feedstock input of around 100 kt per year.
Through our innovative technology, Zincovery has unlocked a solution for sustainable zinc recycling. In furnace dusts, 20-50% of zinc is contained within zinc ferrites – a notoriously difficult compound to recycle zinc from. When acid at sufficient strength and temperature is used to break zinc ferrites – unlocking the zinc from its compound and dissolving it into the acid - the iron compounds co-dissolve. Iron impurities are costly to remove, but a necessary process to achieve a high-purity zinc product.
Zincovery’s biggest technological advantage over the Waelz kiln is a process for breaking zinc ferrite compounds, requiring 70% less energy demand than our main competitors. Our zinc ferrite breaking technology allows for maximum zinc recovery, whilst minimising the dissolution of the iron compounds.
With our inventive technology, we can achieve sustainable zinc recycling which not only reduces costs for our customers, but also provides them with zinc from a clean, green, and circular process. Thus, our technology allows steel mills and recyclers to remove away from the emission-intense Waelz kiln process to an environmentally friendly solution. Additionally, Zincovery’s technology is a viable solution for the waste treatment of smaller and remote steel mills, as it does not require the input scale of a Waelz kiln.
Our prototype (pilot plant) is currently being built, with target operation by March 2023. The pilot plant will demonstrate the scalability of our technology, which has been proven at the lab scale. Operations of our pilot plant will be ramped up to our target throughput (10 kg of zinc metal per day). To stress test the equipment and our methods, we will operate continuously, operating our pilot plant will build the skill set of our team and provide the experience required to scale up the technology further to the commercial scale.
The total global market for recycled zinc is estimated to be US$10bn Initially, Zincovery aims to implement its technology in a number of beachhead markets, namely North-West America (US$91m), Scandinavia and the UK (US$ m), Southeast Asia and Australia (US$166m). Once the technology has been proven in these markets, Zincovery would look to displace the incumbent technology in the larger secondary markets, such as North-East America (US$930m), Europe (US$1.2bn), the Indian subcontinent (US$770m) and China (US$2.8bn).
Contact:
Gabriela Junk
Research engineer, Zincovery
Email: gabriela.junk@zincovery.com